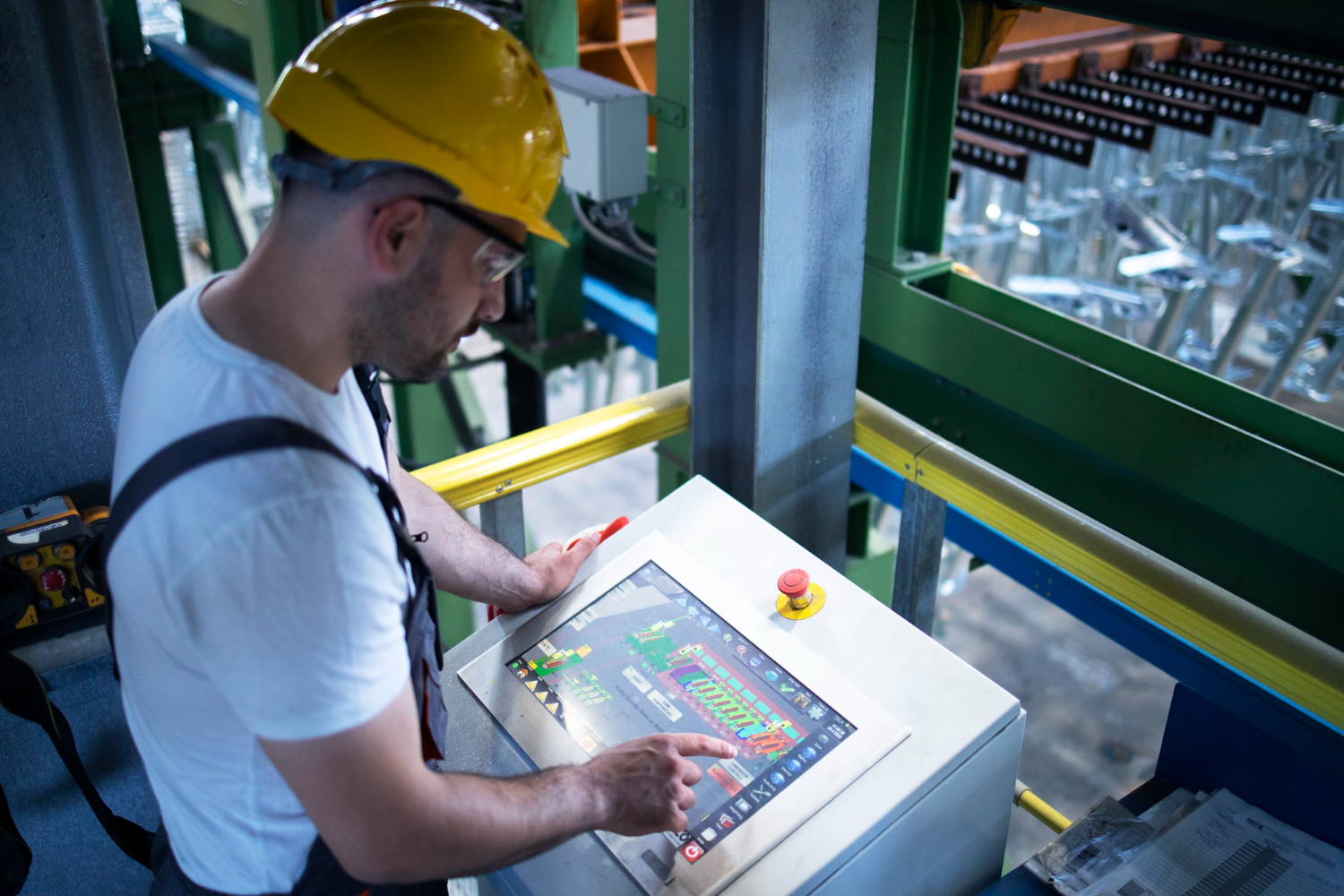
Властелин станков, или Как улучшить процессы на производстве
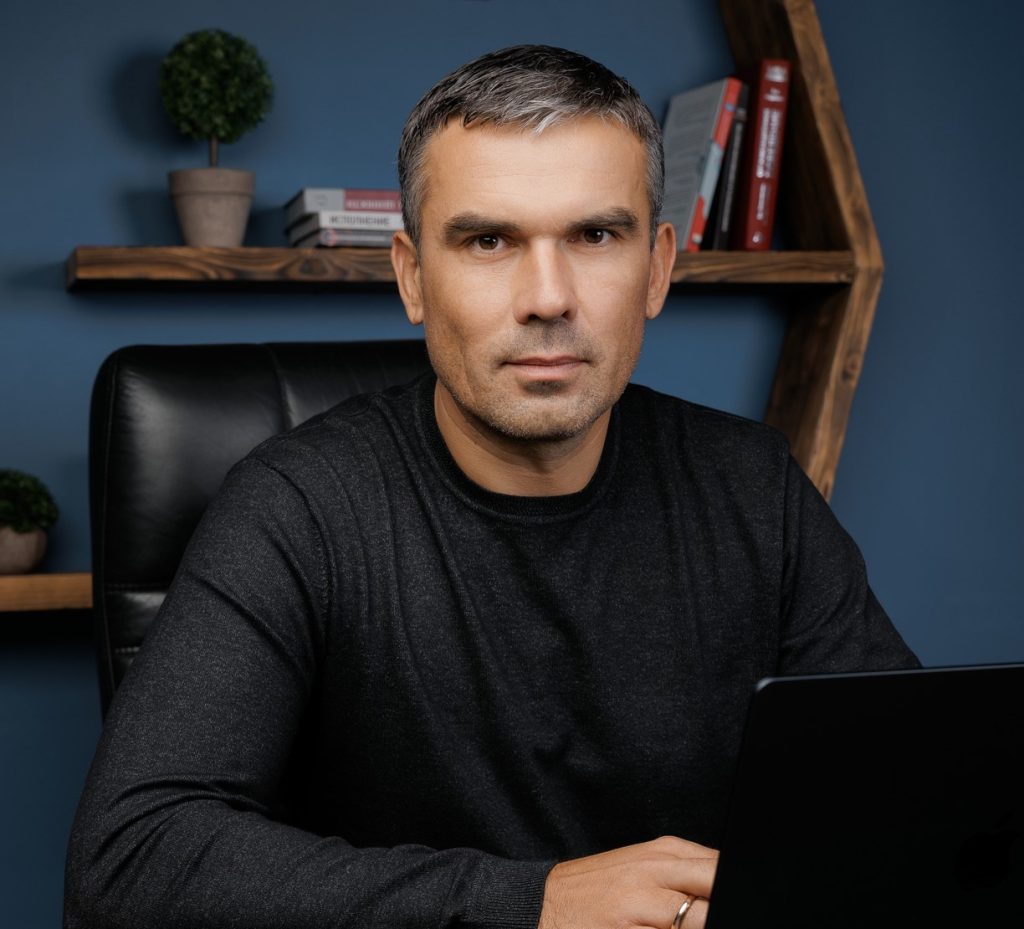
Артем Сеник, основатель и генеральный директор НПО «ЛАБС», создатель аппаратно-программного комплекса для мониторинга и управления производственными процессами «Поток-7»
По статистике, оборудование на промышленных предприятиях в России загружено в среднем на 48% от возможного рабочего времени. Такая ситуация на производствах возникает по разным причинам: здесь и человеческий фактор, и несовершенство технологических циклов и системы управления, и отсутствие контроля за исполнением регламентов, и прочее. В итоге предприятия недополучают прибыль. Многомиллионные вложения в дорогие станки не окупаются. А в некоторых случаях руководители и вовсе идут на покупку нового оборудования при простаивающем старом.
Из-за санкций приобретать европейские и американские станки становится все труднее. Их стоимость, сроки поставок по схемам параллельного импорта из-за сложных логистических цепочек увеличиваются. Отечественных станков не хватает. Остается вариант с оборудованием из КНР, но и здесь есть масса сложностей. Приобретать технику приходится по схемам параллельного импорта, что делает закупки на 20–50% дороже. Зарубежные поставщики, как правило, не имеют представительств в России. Импортерам приходится подбирать поставщика наугад, самостоятельно налаживать доставку и таможенное оформление необходимого оборудования. В этом свете становится крайне актуальным повышение эффективности производства за счет максимально продуктивного использования уже имеющихся ресурсов.
Аппаратно-цифровые решения, созданные для мониторинга загрузки оборудования и оптимизации производственных процессов на промышленных предприятиях и ставшие частью Четвертой промышленной революции (Индустрия 4.0), могут стать выходом из ситуации. Речь идет о принципиально новом подходе к производству, который подразумевает массовое внедрение информационных технологий в промышленность, распространение искусственного интеллекта. Это поднимает значимость автоматизации и цифровизации производственного сектора экономики.
Модели искусственного интеллекта обучаются на больших данных и способны принимать решения на основе накопленного опыта. Технологии на базе машинного обучения могут помочь компаниям анализировать большие объемы информации и выявлять тенденции и закономерности, которые могут быть использованы для определения стратегий и принятия более точных и взвешенных решений. Но для интеллектуального управления промышленными предприятиями необходима достоверная экспертиза, большие данные, а также выявление потенциальных участков, нуждающихся в роботизации.
У большинства предприятий стоит задача не сразу совершить прорыв в Индустрию 4.0, а постепенно внедрять в производство элементы новой реальности. На российском рынке последние несколько лет активно разрабатываются различные системы мониторинга станков и управления производством. В числе программно-аппаратных решений есть технологические платформы в комплекте с цифровыми устройствами IIoT (промышленный интернет вещей), которые можно легко подключить к любому типу промышленного оборудования и передавать информацию через Wi-Fi или Ethernet (так называемые «решения в коробке»). Для установки такой системы на предприятии не требуется производить глубокую интеграцию в промышленное оборудование и станки.
Среднее производство в лучшем случае загружено до 53%. Дирекции завода зачастую не знают потенциала своего производства. Как его узнать? Использовать такие методики контроля, как измерение циклов работы оборудования с помощью секундомера и визуального наблюдения за процессами, в 21-м веке точно неактуально и даже вредно. Методика количественного подсчета показателей тоже не всегда работает, а в некоторых случаях оценки может и навредить предприятию, создав прецедент перепроизводства продукции, накопления невостребованных излишков на складах. Аппаратно-программные решения должны помочь организовать более эффективную систему управления производством, а также собрать достаточно информации для обучения искусственного интеллекта, чтобы он в дальнейшем мог анализировать процессы, делать прогнозы, помогать в принятии решений.
Следующим шагом станет повышение персональной ответственности сотрудников —фиксация несоблюдения технологических циклов, нарушения регламентов проведения работ, в том числе саботажа и разгильдяйства. Персонал, управленцы привыкают к использованию цифровых данных. Формируется система KPI для предприятия, схемы поощрения сотрудников.
Увеличение полезной работы оборудования, уменьшение простоев, повышение персональной ответственности и мотивации персонала — это три основных кита, которые являются локомотивами в рамках концепции Индустрии 4.0.
Изначально многие производственники смотрят на такие аппаратно-программные решения скептически. Они попросту не верят, что этот инструмент позволяет реально видеть, как работает их производство. Но в итоге генеральный директор буквально впервые знакомится со своим производством в реальности. На предприятии меняется система управления. Принятие управленческих решений основывается на базе достоверных цифровых данных. Это позволяет в короткие сроки скорректировать производственно-технологический поток. Повышается прирост производительности предприятия. Возможность промышленного шпионажа также исключается.
Подобные технологические решения позволяют нивелировать проблему контроля, который зачастую трудно эффективно реализовать из-за дефицита человеческих ресурсов и времени. Ведь важно следить за состоянием оборудования, перемещением людей, грузов, транспорта, материалов в режиме 24/7. Для этого на основе проанализированных данных формируется цифровой двойник предприятия. У руководства предприятия появляется возможность прогнозировать эффективность изменений.
Задача Индустрии 4.0 заключается не просто в сокращении издержек, а в переходе к цифровой модели предприятия, на которой можно будет тестировать новые продукты и технологии. Это позволит создавать новейшие производства на базе цифровой модели и реализовывать их в физический продукт, используя оптимальную технологию.
Изображения: Freepik; из личного архива автора
Подписывайтесь на каналы Let AI be в Telegram и «ВКонтакте» — оставайтесь в курсе главных новостей в сфере искусственного интеллекта!